近年来,随着国家经济增速放缓,电力需求增长速度开始下降,由于新能源机组增多、总装机容量增长过快等因素影响,全国600 MW及以上容量的燃煤发电机组的年利用小时数逐年降低。由于机组轮流停机备用造成的机组启停次数逐年增多,以某发电公司为例,2015年机组利用小时数为4 048.33 h,2016年机组利用小时数为3 166.8 h。2015年全厂2台燃煤机组启停次数达11次;2016年由于机组轮停备用造成的机组启停次数达17次,对比2015、2016年,预计机组启停次数会更多,2017年机组利用小时数随之下滑。机组频繁启停导致发电企业成本大幅增加[1]。优化机组启停过程、简化启停操作,使机组快速带上负荷,满足电网对发电机组快速响应的需求,同时减少发电机组启动过程中水、电、煤、油等工质的消耗,减少锅炉超标排放时间,成为电厂降低发电成本、提高盈利能力的重要环节,亦是燃煤机组普遍面临的新课题。
1 机组概述
某发电公司3号、4号机组锅炉采用上海锅炉厂有限公司生产的超临界参数变压运行螺旋管圈、一次中间再热、平衡通风、四角切圆直流燃煤锅炉,汽轮机为上海汽轮机有限公司生产的N600-24.2/566/566的超临界、一次中间再热、三缸四排汽、单轴、双背压、凝汽式汽轮机;发电机为上海汽轮发电机有限公司生产的QFSN-600-2型三相同步汽轮发电机组。机组配套设置脱硫、脱硝和除尘系统,机组达到燃煤机组“近零排放”要求,烟气排放达到或优于天然气燃气轮机组排放标准,即二氧化硫排放浓度不超过35 mg/m3、氮氧化物排放浓度不超过50 mg/m3、烟尘排放浓度不超过5 mg/m3。其中脱硝装置采用选择性催化还原技术(SCR),脱硝装置投入需要其入口烟气温度满足不低于300 ℃的条件,当入口烟气温度低于300 ℃时,延时退出脱硝系统。机组给水系统配置2台50%容量的汽动给水泵和1台30%容量的电动给水泵,其中汽动给水泵除配备高、低压汽源外,还配置有一路采用辅助蒸汽的调试汽源。锅炉制粉系统最下层的A磨煤机配置了等离子点火装置,用于低负荷(250 MW以下)锅炉助燃,保证燃烧稳定。
2 机组启停过程分析
2.1 机组启动过程分析
超临界燃煤机组从启动到并网,需要启动较多的子系统,涉及很多复杂的操作过程,包括锅炉上水、冲洗、升温升压和达到冲转参数,汽轮机的冲转,发电机并网,高压加热器和低压加热器的投运等操作,需要所有专业一起紧密配合才能完成,耗时长,工作任务繁重[2]。甘特图通过活动列表和时间刻度形象地表示出任何特定项目的活动顺序与持续时间,是一种理想的控制工具,在现代项目管理里,被广泛应用。可以使用甘特图来直观地表示出机组启停过程中的所有任务,机组启动甘特图如图1所示。

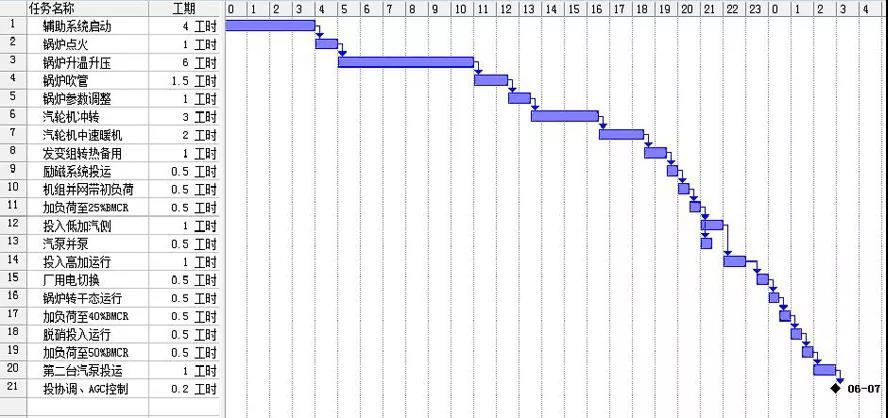
图1 机组启动甘特图
根据机组启动流程及关键节点,列出机组启动过程甘特图,机组启动可以分成21项操作任务。根据某发电公司3号、4号机组目前的机组启动操作票,从机组启动操作开始至机组交电网调度的总工期长达26 h。从辅机启动到厂用电切换的负荷(150 MW)需要21 h,期间需要使用大量启动变压器的高价电量;从锅炉点火开始直至机组负荷250 MW需要20 h,期间锅炉需要大量投油,且由于锅炉排烟温度低,机组脱硝系统无法投运,排放持续超过环保要求。主要存在以下三方面的问题。
a. 由于机组启动时需要稳定燃烧,所以在炉膛点火直至机组负荷250 MW之间,锅炉要投油助燃,出于省油考虑,虽然在投产初期已将AB层4支油枪改造过,单支流量由2.5 t/h改为0.85 t/h,但每小时耗油量仍达到3.4 t,20 h需要使用燃油近70 t。
b. 从2012年GB 13223—2011《火电厂大气污染物排放标准》实施以来,该公司所在的珠三角地区属于严格控制排放的重点地区[3],机组点火开始至机组负荷250 MW之前,机组环保设备受入口温度低限制,脱硝设备无法投入运行,机组启动时NOx排放浓度无法满足100 mg/Nm3的标准,一般只能控制在400 mg/Nm3左右。即从机组点火到机组负荷250 MW这段时间,排放超标,按照相关规定,超标排放需要缴纳相应的排污费用。
c. 机组正常运行时,机组本身的厂用电是机组自供,用电费用相对于发电成本,费用较低。而机组启动时至机组负荷150 MW之前,机组的厂用电通过启动变压器从电网取电,用电费用为0.69元/kWh,相对于电厂自供电,用电成本昂贵[4]。
因此,有必要对机组启动流程进行优化,以缩短机组启动工期,减少机组用油时间,缩短机组启动期间NOx排放浓度超标排放的时间以减少排污费用,缩短机组使用电网电量的时间以降低用电成本。
2.2 机组停运过程分析
同样,根据该公司目前的机组停运操作票,机组停运流程可以分成以下10项操作任务,列出机组停运过程甘特图如图2所示,总工期长达6.5 h。由于机组停运时,在机组250 MW以下时,需要退出高压加热器、切换厂用电、切换给水泵、锅炉转湿态运行等操作,由于操作时间较长,为防止锅炉灭火,也要投油助燃,使用AB层4支油枪,每小时耗油量3.4 t,250 MW以下负荷段都需要投油助燃,约4.5 h,共需要使用燃油近15 t,按5 000元/t计,折合人民币7.5万元。同时,由于机组220 MW以下负荷时间较长,锅炉烟气温度逐步下降至脱硝系统允许运行温度之下,脱硝自动退出,NOx排放浓度也会超标,累计超标排放时间近4 h,产生高昂的排污费用。因此,也有必要对机组停运流程进行优化,以减少机组停运过程的燃油消耗,降低排污费用。
3 机组启停过程优化
3.1 机组启动过程优化
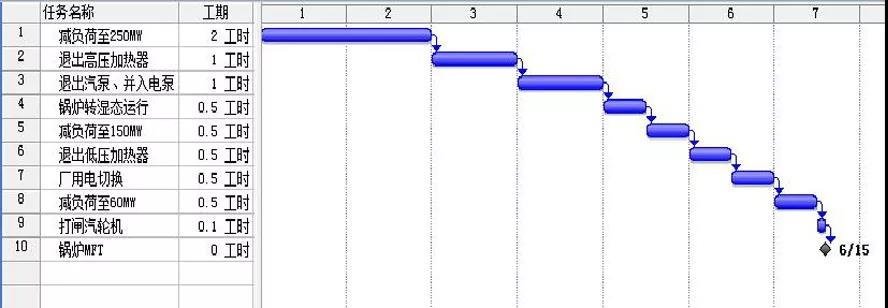

图2 机组停运甘特图
针对机组启动时间过长,启动期间耗电量偏高及排放超标持续时间较长的问题[5],需要对机组启动进度进行优化,缩短机组启动时间。
a. 由于机组启动方式为采用电泵启动,负荷至30%BMCR时冲转1台汽动给水泵并入给水,保持一汽泵一电泵运行至机组负荷300 MW时再并入第2台汽泵,退出电泵。汽动给水泵冲转启动及给水泵切换占用大量操作时间,极大影响机组启动进度。因此,改变机组由电泵启动的方式,采用汽泵全程启动[6],电泵功率8 000 kW,运行电流达700 A,汽泵由辅助蒸汽作为启动汽源,辅助蒸汽由临机提供,由单台前置泵实现锅炉上水,点火时由2台前置泵建立锅炉启动流量,要锅炉升压,前置泵压头无法满足需要时,用辅助蒸汽冲转1台汽动给水泵汽轮机,并停运1台前置泵,实现单台汽动给水泵独立运行,这样可以满足机组50%BMCR负荷前的给水流量需求,另1台汽动给水泵启动后并入给水即可满足机组100%BMCR负荷需求。这样节省了2次给水泵并泵的时间,且启动过程仅前置泵耗电,电流约35 A,功率仅为400 kW左右,能大大节省电耗。同时可以节省启动期间切换给水泵、小机启动等时间。
b. 由于锅炉制粉系统最下层的A磨煤机配置了等离子点火装置。机组启动期间完全采用等离子点火装置助燃,全程不投油。这样要求A磨煤机保持较好的煤种,如神华煤等接近设计煤种的煤,要求煤种挥发分不低、水分不高、热值不低等,保证启动过程燃烧稳定。机组启动时加大A磨煤机暖风器蒸汽通过流量,尽量提高A磨煤机的入口风温,以提高磨煤机出口温度,提高燃烧稳定性;同时要求检修加强火检设备的维护工作,保证锅炉火检设备工作正常。同时要求锅炉火检保护可靠,在机组启动前进行火焰失去保护联动试验[7],实现机组启动全程零油耗。因采用等离子加磨煤机直接点火,给煤机最低煤量为15 t/h,点火初期锅炉金属温升会有些快,在点火初期可将金属温升率适当放大:锅炉金属管壁温度在0~200 ℃控制末级过热器升温速率<5 ℃/min。
c. 机组启动时,给水采用除氧器投入辅助蒸汽进行加热,一般只能加热到100 ℃左右,造成给水温度偏低[8]。严格按温升率≯55 ℃/h和出水温度升率≯110 ℃/h的升温率要求,高压加热器、低压加热器投运需要2~3 h,这也严重制约着机组启动速度[9]。故采用高压加热器、低压加热器随机滑启动方式[10]。再热蒸汽起压后即投入2号高压加热器运行,汽轮机冲转时就将高压加热器、低压加热器投入,跟随汽轮机冲转同步投运。这样能省去单独投高、低压加热器的环节。当主蒸汽压力达到0.2 MPa后,打开高压旁路提高再热蒸汽压力,提前投入2号高压加热器(抽汽汽源为再热蒸汽)的方法,使得给水温度初期能提高到150 ℃以上,锅炉起压后给水温度能逐步升高至200 ℃左右,给水温度的提高,能大大加快锅炉升压速度,节省机组启动时间。同时,由于冲转时汽轮机进汽量大,汽轮机金属温升变快,能有效减少暖机时间。
经过以上优化,将机组冷态启动总时长可以由现有的26 h减少至19 h,即工期减少7 h,缩短26.92%;从锅炉点火到机组负荷40%BMCR由现有的19 h减少至13 h,减少6 h,缩短31.58%,即减少超标排放时长6 h,实现机组启动燃油零油耗。优化后的机组启动甘特图如图3所示。

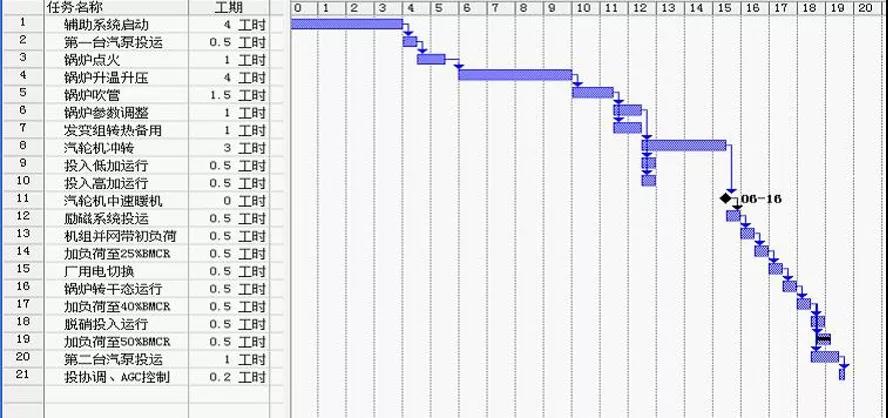
图3 优化后的机组启动甘特图
3.2 机组停运过程优化
根据图2所示机组停运流程甘特图,停机总工期长达6.5 t,耗油量15 t,仅燃油费用就高达7.5万元以上。同时,由于机组250 MW以下负荷时间较长,锅炉烟气温度逐步下降至脱硝系统允许运行温度之下,脱硝自动退出,NOx排放浓度也会超标,累计超标排放时间近4 h,会产生高昂的排污费用。因此,节能方向是减少或者避免使用燃油、减少负荷低于250 MW的时间。根据机组停运流程及关键节点,对机组停运过程进行优化。
a. 去除单独退出高压加热器、退出低压加热器的步骤,采用随机滑退高压加热器和低压加热器,将退出高压加热器和低压加热器的操作并入到汽轮机打闸操作中,即通过打闸汽轮机联动退出。同时由于高压加热器、低压加热器退出时间延后,有利于提高低负荷期间的烟温,保证脱硝的投入。
b. 去除退出汽泵、并入电泵的操作,停机过程全程不使用电泵,保持2台汽泵并列运行至机组解列,此操作需要修改汽泵的最小流量阀定值至250 t/h,保证低负荷时汽泵的运行,满足机组停运期间的给水流量控制需求。
c. 去除锅炉转湿态的步骤,去除250 MW以下常规减负荷的步骤,从负荷220 MW开始,逐台退出烧空给煤机,全程保持最低给水流量不变,随着燃料量的降低,主蒸汽压力同步下降,实现机组负荷同步滑低至60 MW。预计烧空1台给煤机需要4 min,烧空4台给煤机需要20 min左右。最后1台给煤机接近烧空、火焰强度下降时,手动打闸汽轮机、锅炉MFT。烧空给煤机阶段留意燃烧是否稳定,留意火检装置的火焰强度。
经过优化,可将机组停运总时长由现有的6.5 h减少至3 h,即工期减少3.5 h,缩短53.85%,且由于250 MW以下负荷时间短,约为30 min,排烟温度不会降至脱硝允许投入温度之下,保持脱硝系统运行,可以实现脱硝系统全程投入,停机期间可以减少超标排放时长3 h。同时由于低负荷时间很短,250 MW以下负荷段不需要投油助燃,同时,由于简化了停运步骤,停运操作强度大大下降[11]。优化后的机组启动甘特图如图4所示。

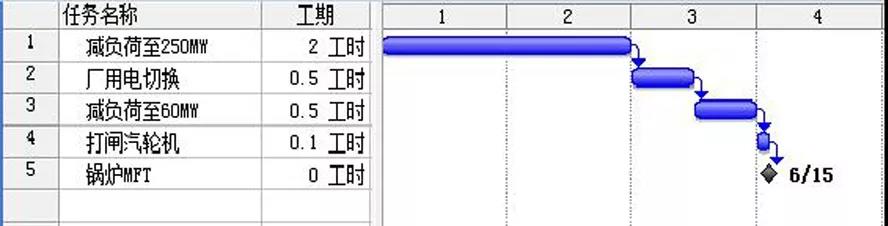
图4 优化后的机组停运甘特图
4 效果评价
机组启停进度优化后,机组启动时可减少6 h超标排放时间,机组停运时可至少减少3 h超标排放时间。我国氨氮污染物排污费征收标准为不低于1.4元/每污染当量,超过限值1倍及以上的处超限值时段环保电价5倍罚款[12]。氮氧化物排污费在火电企业各类大气污染因子排污费中的权重最大,氮氧化物总量减少后可明显减少企业每年排污费的缴款金额。因燃烧1 t煤氮氧化物产生量为19.55 kg,按启动阶段平均燃料量60 t/h计算,可累计节省排放费用为1.56万元。因这9 h超标排放,优化前不但要取消氮氧化物环保电价0.01元/kWh的补贴,还要处以超限值时段环保电价5倍以下罚款,即0.06元/kWh的罚款,按平均负荷100 MW计,电量共计90万kWh,节省环保罚款金额5.4万元。
机组启停进度优化后,机组启动不需要投油助燃时间,单次启动可节省燃油量近70 t,折合金额近35万元。同时由于改由汽泵启动,启动全过程不需要电泵,相比电泵功率减少5 500 kW左右,可有效减少电量消耗约14.3万kWh,由于机组启动期间采用启备变从电网取电,启备变电价按0.69元/kWh计,折合金额近10万元,相当于机组每启动1次,可节省电费支出近10万元。优化后可将机组停运总时长减少3.5 h,可减少超标排放时长3 h。可节省燃油近15 t,折合金额7.5万元。同时由于改由汽泵停运,比电泵功率减少5 500 kW左右,可有效减少电量消耗3.575万kWh,启备变电价按0.69元/kWh计,折合减少电费支出约2.5万元。
机组启停进度优化后,机组启动时节省了给水泵并泵和退泵的操作,减少了带负荷投运高压加热器、低压加热器的操作;机组停运时减少了退出高压加热器、低压加热器的操作,减少了锅炉干、湿态转换的操作。优化后大大减轻了机组启停操作强度,也能提高操作可靠性,降低出错的几率。
5 结束语
实践证明,通过对机组启停进度优化,采用高、低压加热器随机投入缩短了机组启动时间;采用等离子方式启动,全程不需要使用燃油,大大节省燃料成本,同时缩短升温升压时间;采用汽泵启动,取消了电动给水泵与汽动给水泵的切换,缩短了启动时间的同时,还使操作员的工作量大幅减少;机组停运时,能全程保持脱硫系统投运,机组排放能全程满足环保要求。可见,经优化后的机组启停方法,极大缩短了机组启动时间,能有效降低启动成本,预计机组每启停1次,合计可节省成本52.9万元/台次,按该公司2台机组每年启停10次计算,每年可节省成本529万元,具有显著的经济效益和环保效益。
参考文献:
[1] 赵小利,李晓明.竞争机制下的火电机组启停计划的优化[J].电力科学与工程,2003,19(3):11-15.
[2] 肖大雏. 控制设备及系统[M].北京:中国电力出版社,2006.
[3] 郭逢泽,高 帅.电厂运行优化与节能降耗措施研究[J].科技创新与应用,2015,5(20):115.
[4] 谷文超.电机节能降耗技术和方法探讨[J].化工管理,2016,29(33):128.
[5] 顾伟飞,樊印龙,钱晓峰,等.600 MW汽轮发电机组无电动给水泵启动[J].发电设备,2006,20(5):345-347.
[6] 宋 博.600 MW火电机组节能降耗研究[J].科技风,2014,27(4):53.
[7] 张 健.300 MW火电机组热力系统的冷态启动优化[J].科技致富向导,2012,20(2):316.
[8] 王 丹.火力发电厂节能措施简析[J].科技创新导报,2015,12(21):237-238.
[9] 雷贵祥.发电厂热能动力系统优化与节能改造研究[J].资源节约与环保,2015,33(7):3.
[10] 李 琼.大型火电机组启停过程的安全与节能[J].科技与企业,2012,21(21):269.
[11] 吴兴智.火力发电厂汽轮机组节能降耗措施探讨[J].江西建材,2017,37(5):202-203.
[12] 高志远.百万机组火电厂节能降耗的运行分析与措施[J].山东工业技术,2016,35(17):62.